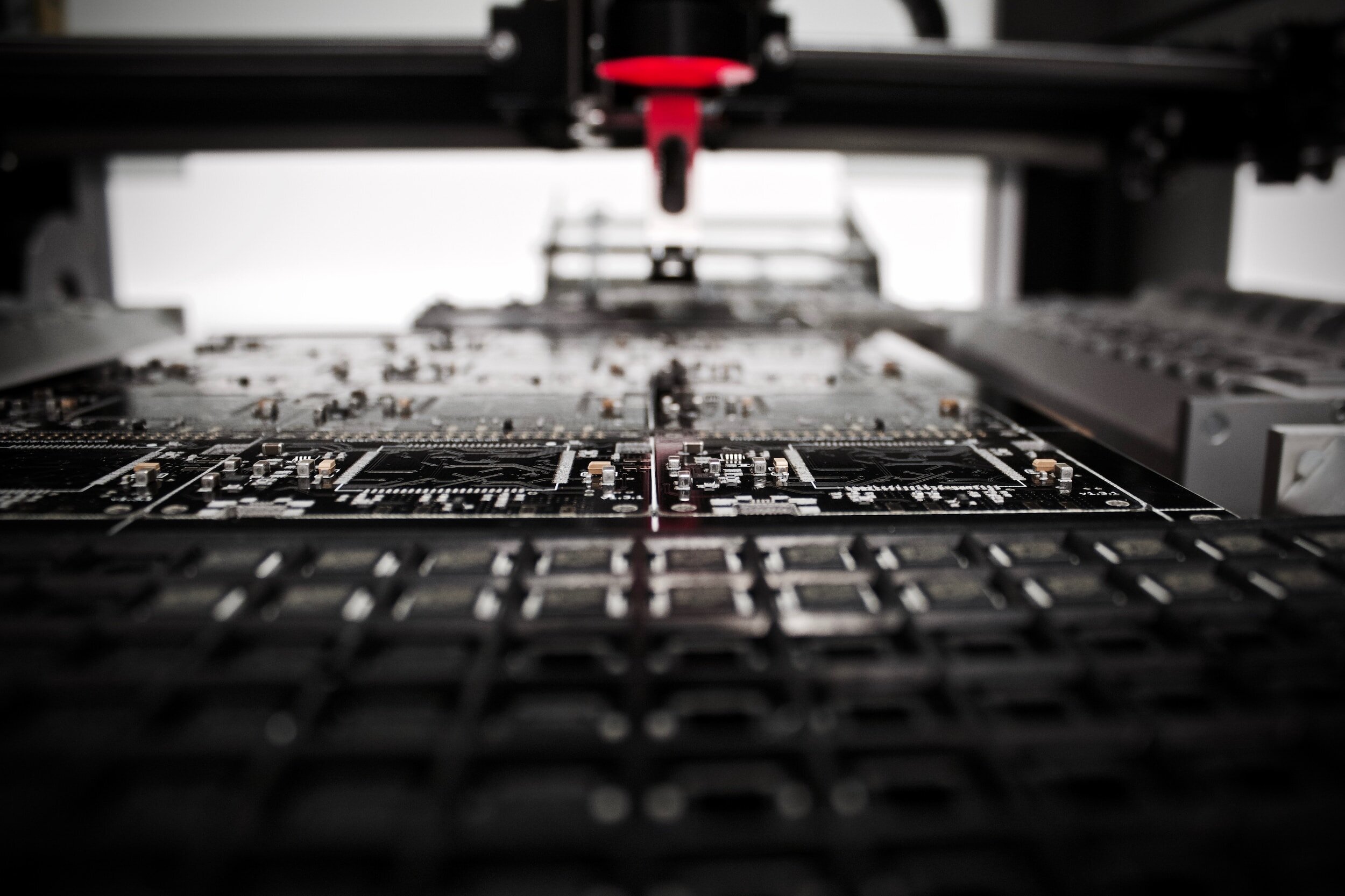
Motors — Magnet Free Future?
Switched Reluctance
Switched Reluctance motors are a distinct category of electric motors, characterised by their simple yet robust design and unique operational principle. Unlike traditional electric motors that rely on magnets and coils they leverage the concept of reluctance and operate through the controlled switching of phases to create a magnetic path of least reluctance, resulting in efficient and precise rotation. SR motors offer high power density, ruggedness, and the potential for cost-effective manufacturing due to their simpler construction. These attributes make SR motors suitable for a wide range of applications where performance, reliability, and energy efficiency are key.
Synchronous Reluctance
Synchronous Reluctance motors represent a sophisticated class of electric motors designed to combine the benefits of both synchronous and induction motor technologies. SynRM motors offer high efficiency at a wide operating speed range, making them suitable for applications where precise control and energy savings are essential, such as in industrial pumps, fans, and compressors. The evolving emphasis on energy efficiency and sustainability has fueled interest in SynRM motors as a viable and environmentally friendly option in the realm of electric motor technologies.
Field Excited Rotor/Stator
A field excited motor allows the rotor and stator windings to be separately controlled, allowing for greater flexibility in adjusting performance characteristics. Such motors find applications in various industries, such as machine tools, robotics, and electric vehicles, where their ability to deliver high performance and precise control make them advantageous for demanding and specialised tasks.
Flux Switching
Flux Switching Motors represent an innovative class of electric motors. The design of flux switching motors allows for improved efficiency, reduced energy losses, and enhanced power density. Additionally, their simplicity, robustness, and potential for high-torque applications give the capacity to address challenges and optimise performance in various industrial and automotive applications.
Motors — Rare Earth, High Power Density
Surface Permanent Magnet
SPM motors find applications in various industries, including electric vehicles, robotics, and industrial machinery, where their high power density, reliability, and precise control capabilities make them well-suited for demanding tasks. The direct interaction between the surface-mounted magnets and the stator windings results in efficient energy conversion and contributes to their growing popularity.
Internal Permanent Magnet
Internal Permanent Magnet motors have gained prominence in the electric motor landscape as they offer a compelling combination of compact design, energy efficiency, and high-performance characteristics. Their configuration allows for a more compact and efficient design, reducing the air gap between the rotor and stator. The arrangement of internal magnets enhances the magnetic field interaction, leading to improved torque and power density.
High Speed Motors
The ability of high-speed electric motors to deliver swift and precise rotational motion makes them integral in applications where speed and responsiveness are paramount, contributing to advancements in various technological fields. Technelec has motors rated to speed in excess of 200,000 rpm. The construction of such high-speed electric motors involves specialised materials and precision engineering to withstand the centrifugal forces and thermal challenges associated with elevated speeds.
Traction Motors
Traction motors take various forms including induction ,permanent or synchronous - each with its own advantages. The efficiency and performance of traction motors directly impact the overall energy efficiency and range of electric vehicles. As the automotive industry continues to transition towards electrification, the development and optimisation of traction electric motors become increasingly important in shaping the future of sustainable and eco-friendly transportation. The below motor utilises the carbon sleeve technology and an IPM giving a high power density whilst being able to withstand high speeds for 150kW+ machines.
Inverters — High efficiency or low cost?
Automotive Traction Inverters
Technelec has ASIL B and ASIL D designs for both 800V or 400V automotive applications ready to be transformed into your application requirements.
Automotive Compressor Inverters
Technelec offer compact inverter designs with high switching speeds for applications such as E-turbos, Hydrogen Fuel Cell Compressors and Lidar Sensor Cleaners
Industrial/Domestic Applications
From Electric Boats and Heat pumps to AC-DC Bidirectional converters for Battery storage, Technelec have several long standing industrial partners across a range of applications.
Low Voltage Drives
Technelec has worked with low voltage brushless drives for over 25 years, pioneering our sensorless control. Such drives are low cost, easy to manufacture and highly efficient.
Motor Control — Automotive, Sensorless, Low Cost?
Automotive Applications
Automotive electric motors must efficiently deliver torque across various speeds to ensure smooth acceleration and performance in EVs.
Sensorless Motor Control
By leveraging advanced algorithms and signal processing techniques, Technelec’s sensorless motor control systems can estimate the rotor position and speed based on the motor's electrical characteristics. Not only streamlining the design and manufacturing process, but also reducing cost and increasing overall robustness in various electromechanical applications, where precise control is essential.
Efficient Code
Optimised code ensures precise speed and torque control, contributing to smooth motor operation. Technelec’s software facilitates effective fault detection, preventing system failures. The need for sophisticated and well-maintained software is paramount for achieving optimal performance, reducing energy consumption, and ensuring system longevity.
Data Analysis
Analysing data during motor operation provides insights into performance, efficiency, and potential issues. It helps identify optimal control strategies, enhancing energy efficiency. Additionally, effective data analysis aids in predictive maintenance by detecting early signs of wear or faults, preventing unexpected system failures. At Technelec, built in self diagnosis and data analysis is made possible with our testing and fault checking software. From production to in-field use, we can track when and how a product is faulty.